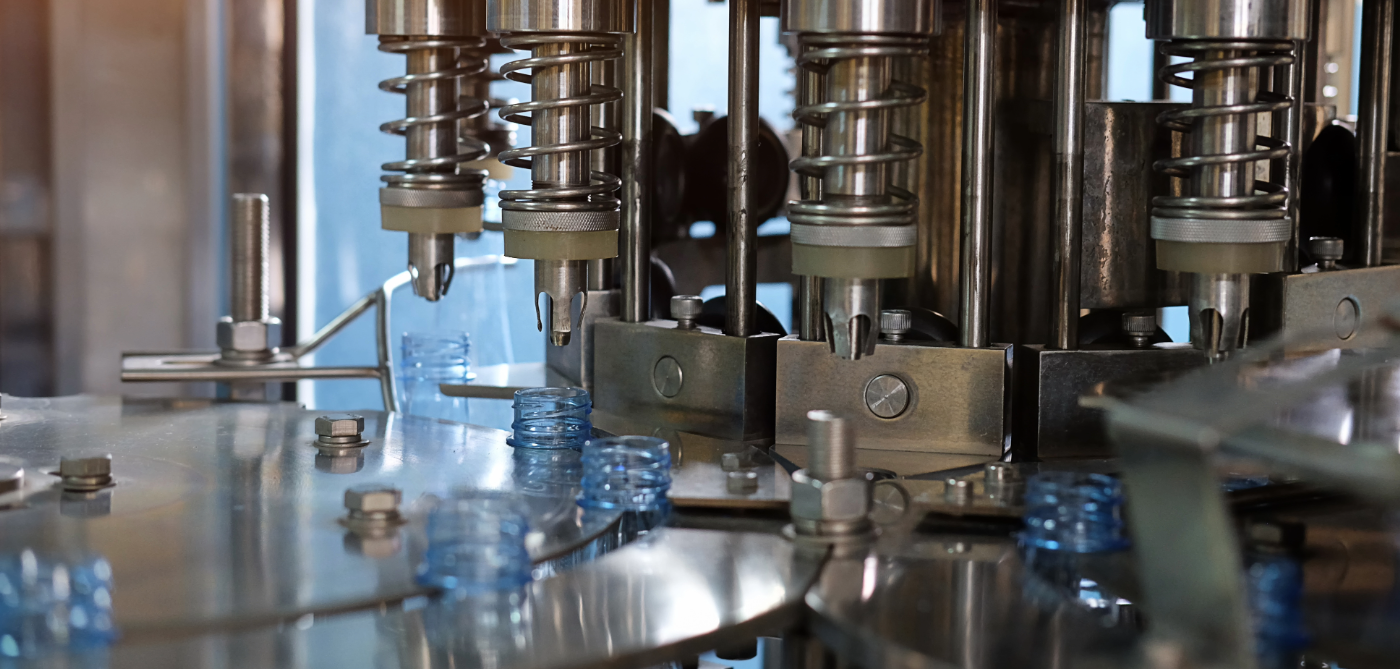
How Air Quality Impacts Plastic Injection Molding and Product Integrity
The Overlooked Factor in Plastic Injection Molding
Many factors influence plastic injection molding, from mold design to material selection. One element that often gets overlooked? Air quality.
Contaminants in the air—like moisture, oil, and fine particles—can lead to product defects, increased waste, and unnecessary production delays. For businesses that rely on precision, controlling air purity is essential.
Why Air Quality Matters in Plastic Injection Molding
Air plays a major role in shaping and cooling products during plastic manufacturing quality control. If the air isn’t clean, manufacturers face challenges such as:
- Surface Defects – Dust and oil in the air can cause blemishes and inconsistencies in the finish.
- Weak Product Structure – Contaminants interfere with material bonding, creating brittle or faulty products.
- Higher Rejection Rates – Inconsistent air pressure and unfiltered contaminants increase failed quality tests.
- Machine Wear and Tear – Dirty air leads to clogged lines, corrosion, and costly maintenance.
Upgrading to industrial air systems in plastics helps prevent these issues.
What Causes Contaminated Air in Plastic Production?
Manufacturers who depend on air quality in plastic production must watch for several types of contamination:
- Oil Residue – Older compressors often leak oil, which can mix with plastic materials.
- Excess Moisture – High humidity levels cause condensation, affecting the texture and durability of plastic products.
- Airborne Particles – Dust and fine debris from the factory environment can disrupt molding processes.
- Microbial Growth – In industries like medical plastics, sterile conditions are necessary to prevent contamination.
Manufacturers can maintain higher production standards by improving air filtration in factories that produce plastic.
How to Keep Air Quality High in Plastic Injection Molding
To maintain contaminant-free plastic molding, manufacturers should take the following steps:
-
- Install High-Quality Filtration – Advanced filters remove oil, moisture, and dust before they reach critical equipment.
- Schedule Routine Maintenance – Regular system inspections help detect contamination before it becomes problematic.
- Use Dry Air Technology – Low-humidity air prevents condensation that can weaken plastic materials.
- Maintain Consistent Air Pressure – Stable pressure ensures even mold filling and uniform cooling.
- Monitor Air Purity in Real-Time – Automated tracking systems help manufacturers react quickly to any issues.
How Pneumatic Systems Improve Plastic Manufacturing
Pneumatic systems in plastic production help regulate air flow, remove impurities, and maintain clean operations. Businesses that invest in airborne impurity prevention in production benefit from:
- Better product consistency
- Less downtime for maintenance
- Fewer defects and material waste
- Longer-lasting equipment
Experts in air system efficiency in manufacturing can help manufacturers find the right setup for their needs.
Selecting the Right Air System for Plastic Injection Molding
The best air system optimization for quality assurance depends on several factors, including:
- Industry Standards – Meeting ISO 8573 air quality requirements.
- Production Growth – Choosing systems that can scale with increasing demand.
- Energy Savings – Upgrading to modern systems that cut operational costs without lowering performance.
When you work with industrial air system maintenance professionals, manufacturers avoid costly mistakes and improve production efficiency.
Reliable Air Solutions for Plastic Injection Molding
Arizona Pneumatic provides manufacturers with customized air solutions that help reduce defects, increase efficiency, and improve air purity standards for plastic manufacturing.
Looking for Better Air Quality in Your Facility?
Get in touch to learn how our air systems can support your production line. Call (480) 637-4438 or visit Arizona Pneumatic to explore our solutions and products.