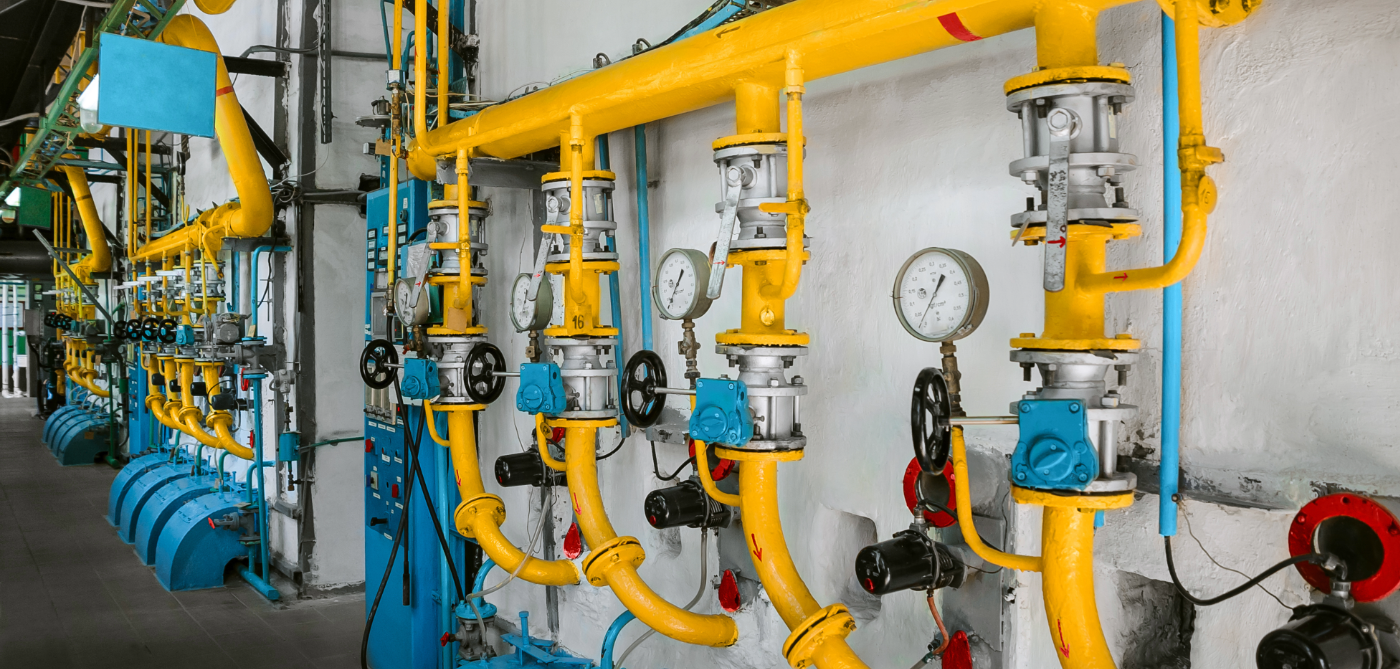
Optimizing Compressed Air Systems for Quality in High Ambient Conditions
The quality of compressed air systems is consistently overlooked and rarely proactively managed within industrial manufacturing operations—until it’s too late. This is particularly true in Arizona and Nevada, where high ambient conditions like extreme temperatures create additional challenges for compressed air systems. This article will address the importance of understanding dew point specifications and working with a Compressed Air and Gas Institute Certified Compressed Air System Specialist in designing a properly sized refrigerated air dryer for high ambient conditions.
Understanding Compressed Air Systems and Their Importance
A compressed air system plays a critical role in powering machinery, tools, and equipment within industrial operations. The system compresses air into a tank, which is then used to drive various processes. However, the quality of the compressed air in these systems is crucial for smooth operations. Without proper maintenance, contaminants like particulates, water, oil, and microbiological content can accumulate, leading to inefficiency and potential damage to sensitive equipment.
Key components of compressed air systems include:
- Compressors: These increase the air pressure necessary for the system to function.
- Dryers: These remove moisture from the air, preventing damage to equipment.
- Filtration Systems: These clean the air to prevent contaminants from compromising the system’s efficiency.
A key performance indicator of compressed air quality is found within ISO 8573-1-2010, the food and beverage industry-accepted British Compressed Air Society (BCAS), or Safe Quality Foods (SQF) standards. When discussing compressed air quality, we are primarily concerned with particulates, water, oil, and increasingly, microbiological contents. To meet these standards, customized air solutions are often needed, especially for systems facing high ambient conditions.
Challenges in High Ambient Conditions and Their Impact on Compressed Air Systems
In places like Arizona and Nevada, where the heat is extreme, compressed air systems face their own set of challenges. Extreme conditions—such as temperatures exceeding 100°F—can significantly affect system performance, leading to higher energy consumption, more wear and tear, and a shorter lifespan for the system.
The main challenges with high ambient conditions include:
- Moisture buildup: In hot temperatures, moisture tends to accumulate within the system, and it can condense inside the pipes. This excess moisture can significantly affect the quality of compressed air, leading to contamination and potentially costly damage to the equipment.
- Reduced system efficiency: As compressed air systems operate less efficiently at higher temperatures, operational costs rise, and system output decreases.
At Arizona Pneumatic, we provide customized air solutions to address these high-ambient challenges, ensuring that your compressed air systems continue to operate efficiently and reliably no matter the temperature.
Watch Out for Improper Refrigerated Air Dryer Sizing
One of the other critical issues in these environments is the improper sizing of refrigerated air dryers. Non-certified salespeople have historically been negligent when it comes to correctly sizing dryers for high ambient conditions in Arizona and Nevada. This negligence often leads to undersized dryers that cannot handle the high temperatures, resulting in poor system performance, moisture buildup, and increased maintenance costs.
This negligence can be avoided by working with CAGI-certified specialists who understand the importance of proper sizing for high ambient conditions. Improper sizing of refrigerated air dryers can result in compressed air quality falling to Class 6 or even Class 7, which is commonly referred to as “liquid.”
How Arizona Pneumatic Optimizes Compressed Air Systems for High Ambient Conditions
At Arizona Pneumatic, we are experts in designing compressed air systems that are optimized for high ambient conditions. Properly sized refrigerated air dryers are key to ensuring consistent dew point levels and preventing moisture buildup, which can severely impact system performance.
A properly sized refrigerated air dryer plays an important role in managing ISO 8573-1 standards for compressed air quality. These systems are typically designed to achieve Class 4 (<38°F) or Class 5 (<45°F) dew points. However, understanding the upper limits of each dew point class is essential. Failure to size a refrigerated air dryer correctly often leads to moisture downstream in the system.
A properly sized refrigerated air dryer is essential for the hottest days of the year. Without it, a compressed air system is at risk of failing to meet quality standards, which can result in costly repairs and downtime.
The Importance of Proper Sizing and Dew Point Management in Compressed Air Systems
Making sure the correct dew point is maintained in compressed air systems is essential for efficient and safe operations. Most industrial compressed air systems are designed to operate within the ISO 8573-1 Class 4 (<38°F) or Class 5 (<45°F) dew point specifications. However, understanding the upper limits of each dew point class is critical to maintaining consistency. The difference between “less than” and “equal to” dew points is important when striving to achieve consistent air quality.
When dryers are undersized, or when proper dew point management is ignored, moisture can accumulate, leading to Class 6 or even Class 7 compressed air quality—referred to as “liquid” air. This will inevitably result in operational disruptions, increased maintenance, and equipment damage.
Case Study: Customized Air Solutions for an Industrial Glass Tempering Facility
A prime example of how Arizona Pneumatic delivers customized air solutions involves an industrial glass tempering facility in Arizona. During the hot summer months, when temperatures regularly exceeded 100°F, the system’s air receiver, which was supposed to be dry, would fill with moisture, indicating something was wrong.
The cause? An undersized refrigerated air dryer that couldn’t handle the high ambient conditions. After contacting Arizona Pneumatic, the client worked with a CAGI-certified specialist to design a properly sized refrigerated air dryer solution, along with the necessary redundancy and filtration.
The solution included:
- A properly sized refrigerated air dryer designed to meet the high ambient temperatures of Arizona.
- Redundancy and filtration to ensure long-term reliability and prevent future moisture issues.
- Digital dew point monitoring for ongoing, proactive management of compressed air quality.
As a result, moisture buildup was eliminated, and the facility no longer faced issues during the high ambient months. The risk of dryer failure and costly downtime was also minimized.
Proactive Management of Compressed Air Systems
As the saying goes, “How can we manage that which we cannot measure?” This is where digital dew point monitoring becomes a game-changer. Over the last few years, there has been a shift toward more diverse, technology-driven facility managers who understand the value of real-time measurement and management. Digital dew point monitoring has become the proactive standard for managing compressed air quality, helping facility managers maintain consistent dew points.
By adopting digital dew point monitoring, businesses can:
- Reduce downtime: Timely identification and resolution of issues prevent unexpected breakdowns and production halts.
- Extend system longevity: Continuous monitoring helps ensure that systems perform efficiently, reducing wear and tear.
- Improve operational efficiency: Proactive management reduces energy consumption and increases system productivity.
Properly sizing your compressed air systems, understanding dew point specifications, and adopting proactive monitoring systems are all crucial for maintaining performance—especially in high ambient conditions. Arizona Pneumatic provides customized air solutions that optimize your compressed air systems, helping to prevent issues before they arise and ensuring long-term reliability.
If you’re facing challenges with your compressed air systems, or if you simply want to optimize your system for better performance, contact Arizona Pneumatic at (480) 637-4438 or email us at info@arizonapneumatic.com. Let us help you maintain a reliable, efficient compressed air system that will serve your business needs for years to come.
Personalized Business Solutions
Arizona Pneumatic is the trusted leader in the industry of compressed air systems. Independently owned and operating in the Southwest since 1977, our foundation is the cornerstone of trust for clients seeking reliable solutions for their compressed air system needs. With a steadfast commitment to excellence, we specialize in industry-certified sales, service, design, and installation of compressed air systems tailored to the unique needs of businesses of all sizes.
Arizona Pneumatic delivers decades of experience in the design, sales, installation, and service of compressed air systems. Our dedicated team of professionals possesses extensive knowledge that serves a diverse range of industries that includes pharmaceutical, food, beverage, power generation, laboratory, aerospace, defense contractors, education, industrial, and high-tech manufacturing industries.
When you choose Arizona Pneumatic, you’re choosing a partner dedicated to the success of your business. Our commitment to excellence, industry-certified solutions, and personalized service make us the preferred choice for air compression systems. Experience the Arizona Pneumatic advantage – where expertise meets innovation to power your success. Contact us today to receive a consultation with one of our experts. Call (480) 894-9805 today to schedule!